Situation
Our customer is a company specializing in the manufacturing of sapphire watch glasses.
It is recognized as a trusted supplier for luxury watch brands, fully meeting their high standards of quality and precision.
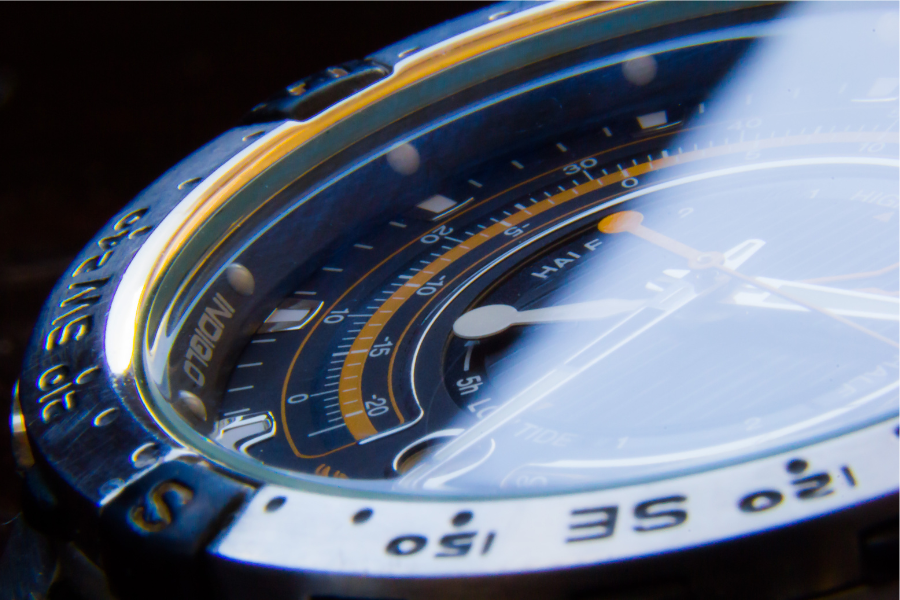
Challenge
Cosmetic inspection represents a major challenge for our customer.
This control is performed in a clean room, by operators whose task is to visually inspect each watch glass with the naked eye and a magnifying glass. The aim is to detect cosmetic defects: machining defects, scratches and defects in the material.
The major problem lies in skills management for this task.
The work is perceived as repetitive, unattractive and in a restrictive environment. Ensuring continuity when operators retire or are absent for a long period of time is a real challenge. Training a new operator represents an investment of several months.
Our customer has explored different technological alternatives available on the market, but none of them proved economically viable or achieved the desired level of quality.
Solution
Intrigued by the promise of automated inspection with our QualiLENS®200, our customer decided to evaluate the technology in more depth.
A set of watch glasses samples, representative of the most common defects encountered in their production, was collected and a test campaign was initiated.
The aim was to prove the capability for the QualiLENS® technology to automatically detect and classify defects – including material defects, which are particularly difficult for operators to detect.
Tests with QualiLENS®200 proved successful.
This solution uses an optical technology based on phase-shifting deflectometry.
The system generates processed maps highlighting variations and anomalies in the surface of materials in a more relevant way than conventional imaging technologies.
This goes beyond visualization of defects. Software processing of the image using proprietary algorithms enables defects to be identified, labelled and classified in various categories: machining defects, scratches, inclusions, bubbles, haze and more.
Outcome
Convinced by the tests, our customer decides to purchase a first machine to customize and validate it, on an industrial scale, in his production process, in collaboration with our team of experts.
The deadline was met. The machine achieves a 100% detection rate on the reference batch, accurately identifying all expected defects and surpassing operators’ ability to detect defects.
QualiLENS®200 thus makes it possible to automate a tedious inspection process while improving the quality and accuracy of cosmetic inspection.
Our customer has placed orders for additional machines to gradually equip all its production lines and roll out the automation project.
Machines are integrated into the automated process, with a robot handling the loading and unloading of parts for inspection.
Although the project is still in production implementation step, our customer already foresees a significant improvement in quality control efficiency and resource savings thanks to this automation.
We’ve found a reliable solution to address the subjectivity of cosmetic inspection and reduce costly over-quality.
It also allows us to clarify quality expectations with our customers based on objective criteria, thus limiting debates.