Situation
Our customer is a leading manufacturer of glazing systems.
They have a dedicated department for producing special glazing for the aerospace industry, including cabin windows for aircrafts.
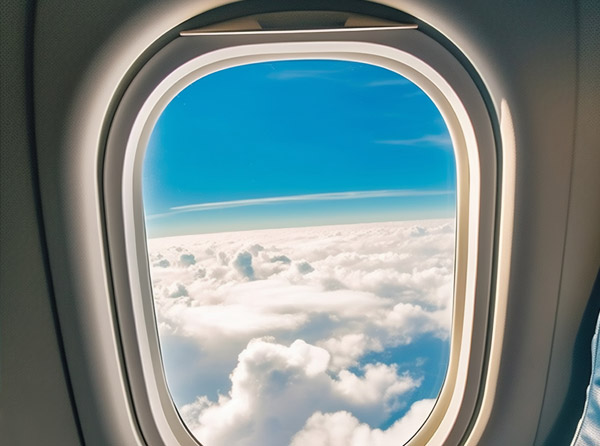
Challenge
The quality control of cabin windows involves detecting cosmetic defects, such as scratches, and optical defects, such as distortion. The traditional method used in the aerospace industry relies on visual inspection by an operator who assesses surface defects and observes a reference grid through the cabin window. If the grid pattern appears distorted, it indicates a distortion in the cabin window. This is known as the “slope method.”
This subjective method often leads to debates about the conformity of the parts between the supplier and the aircraft manufacturer.
To avoid these discussions and the resulting penalties, our client sought an objective method with measurable criteria.
Solution
Experts from V-OPTICS collaborated with our customer’s team to develop a complete automated quality control system in production.
We based our work on the QualiLENS® 400 system, an effective solution for inspecting large transparent parts.
The QualiLENS® 400 is an automated inspection system, based on phase-shifting deflectometry, to produce accurate processed maps highlighting surface and material defects. This solution enables defects to be automatically identified, labelled and classified.
Moreover, we developed a specific module to assess distortion as well as a custom mounting system suitable for inspecting cabin windows.
Many testing and measurement campaigns were conducted to help the customer to prove to the aircraft manufacturers that this innovative system could be correlated with the “slope method,” while offering superior precision and objectivity. According to the standard, the final decision to accept the part must still be made by a human operator. Therefore, the system is used as an aid to the operator for making the diagnosis.
Outcome
The system was developed and validated in the laboratory with samples and then transferred to the factory. It is currently being integrated into the production line.
The results provided by the QualiLENS® 400 not only correlate with the traditional method but they also surpass it.
On one hand, the system delivers a verdict based on indisputable quantified measurements. On the other hand, it detects defects that the traditional method missed.
The main benefit perceived by our customer is to have found an objective method of quality aligned with their customers’ expectations. This facilitates the customer-supplier relationship and reduces the risk of disputes.
The implementation tested during the development of this new cabin window is a successful first step. This paves the way for deploying this inspection technology to other glazing systems in their current ranges.
We were impressed by the sensitivity of the system and its ability to detect very fine distortions. The system detected defects that we have missed with the traditional method.