Situation
Our customer is one of the world’s leading manufacturers of contact lenses.
They provide eye care practitioners with a large portfolio of specialty contact lenses.
Specialty contact lenses are soft or rigid custom designed lenses that fit the individual cornea shape and specific prescription.
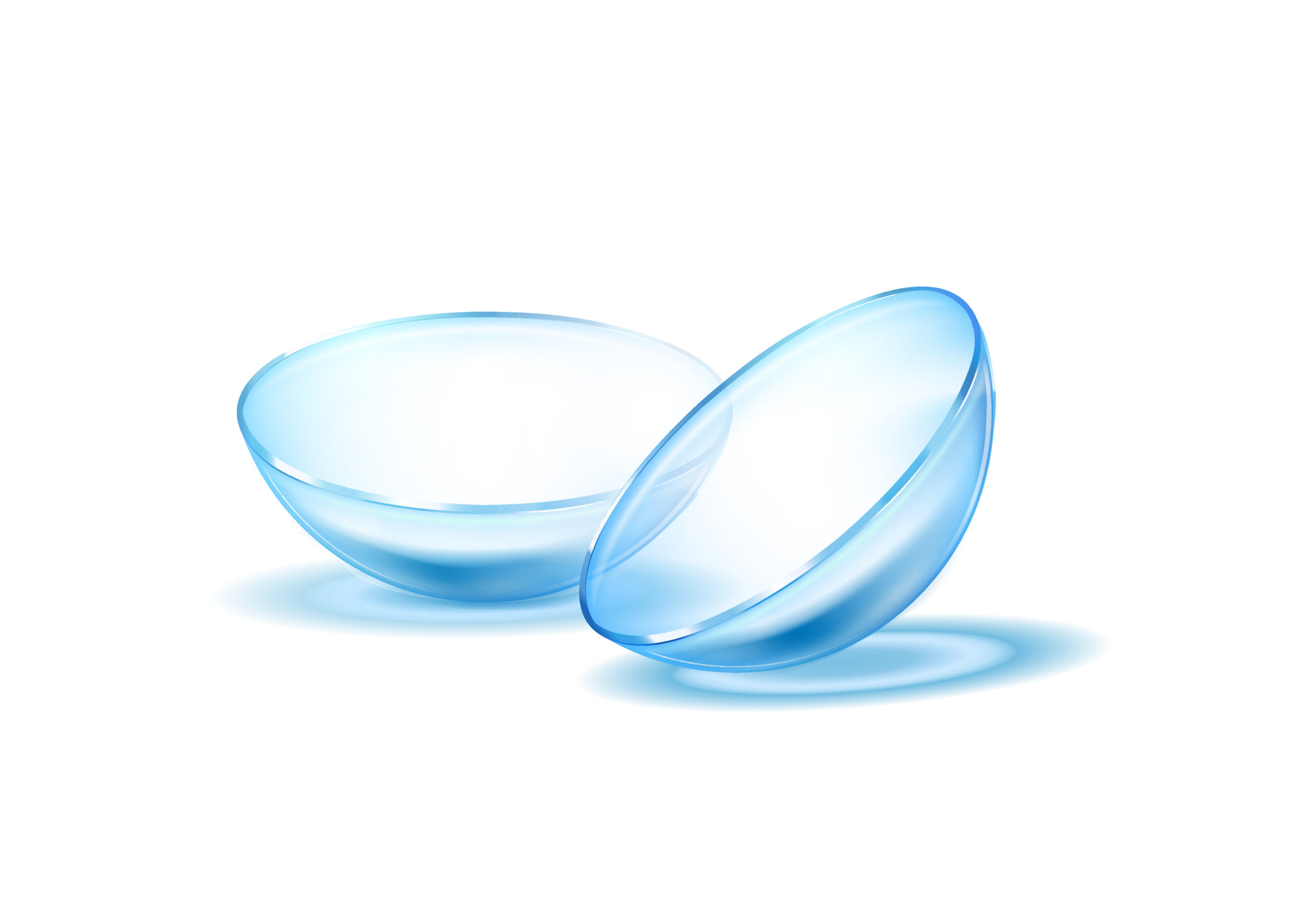
Challenge
Surface defects are carefully controlled to ensure that the lenses meet the required quality standards.
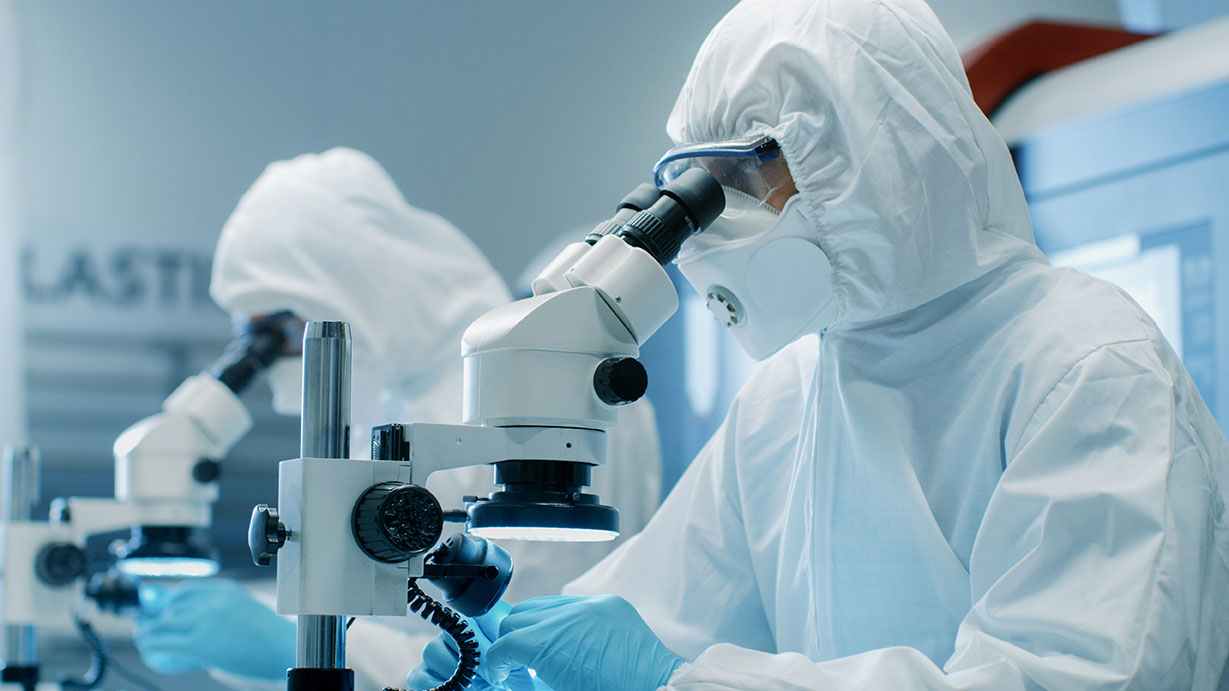
However, the current manual cosmetic inspection process, relying on skilled operators to identify defects using binoculars, leads to too much variability in an industrial context.
Tests revealed that only 30% of lenses were diagnosed consistently across 3 consecutive measurements of the same set by the same operator.
This highlights the almost random nature of control operation performed by inspectors and the need to improve the consistency of assessments.
Solution
Our customer decided to evaluate the technology of the QualiLENS® 100 to check how it could enable operators to be more consistent in their inspection.
QualiLENS® 100 is an automated inspection system, based on phase-shifting deflectometry, to produce accurate processed maps highlighting surface and material defects.
This solution enables defects to be automatically identified, labelled and classified.
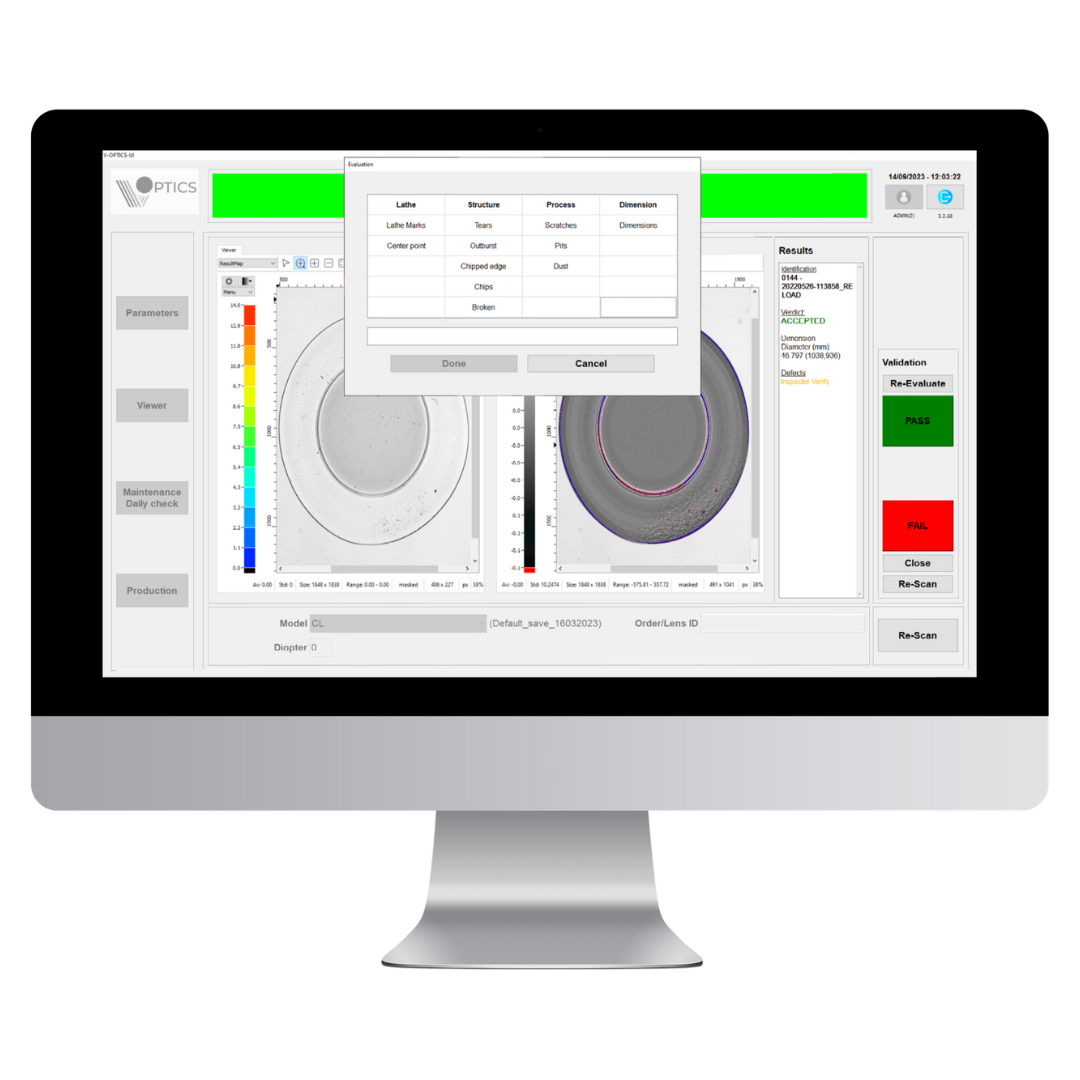
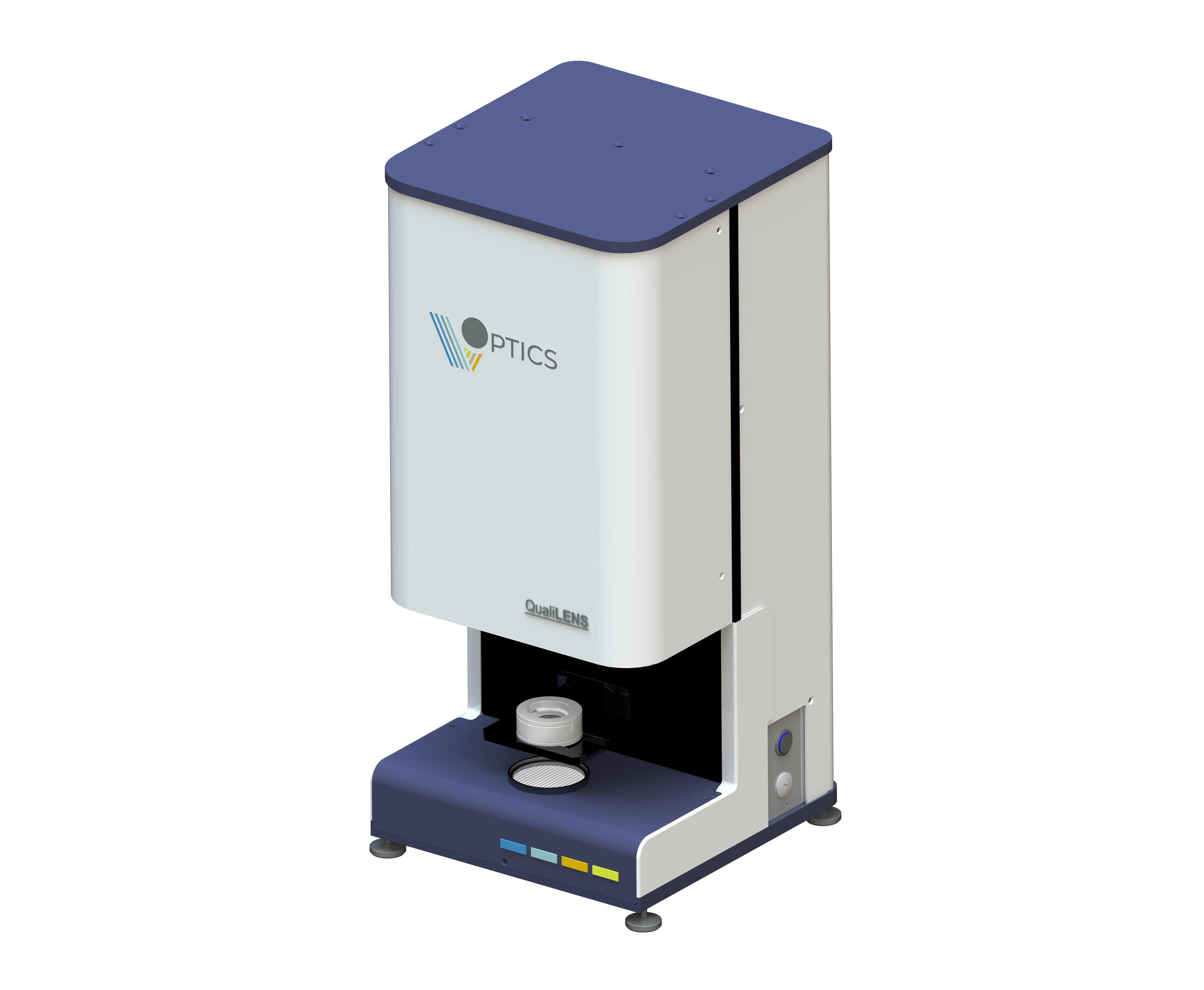
Rather than opting for full automation, the initial focus was on the use of the viewer mode. With the viewer mode, operators can visualize Amplitude and Raw maps side by side on the screen, enabling them to detect the tiniest defects such as lathe marks, scratches, chipped edges, and more.
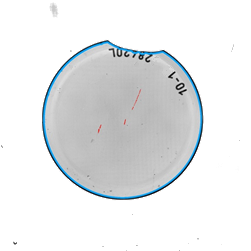
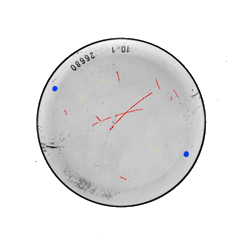
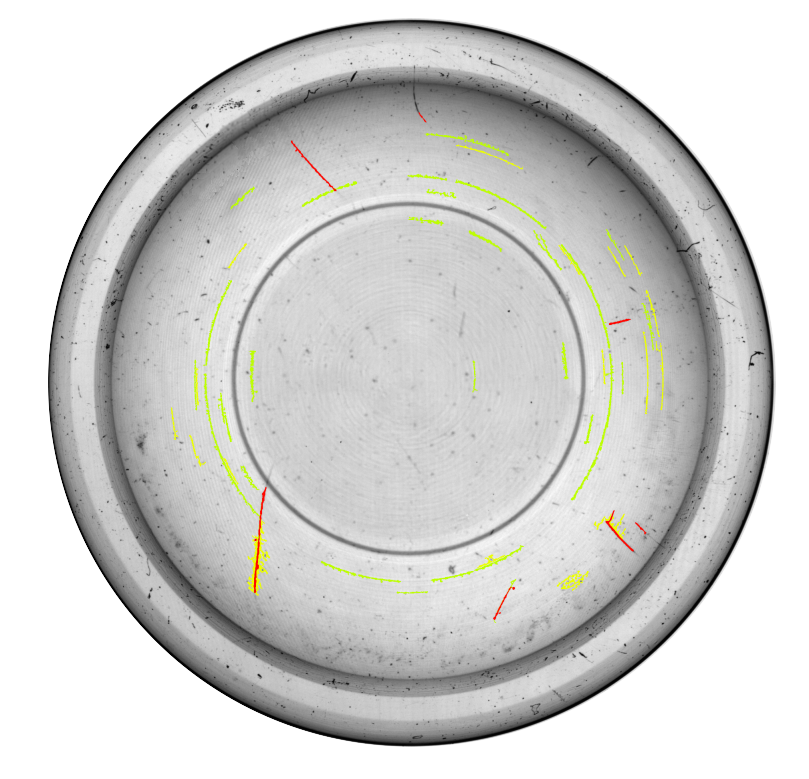
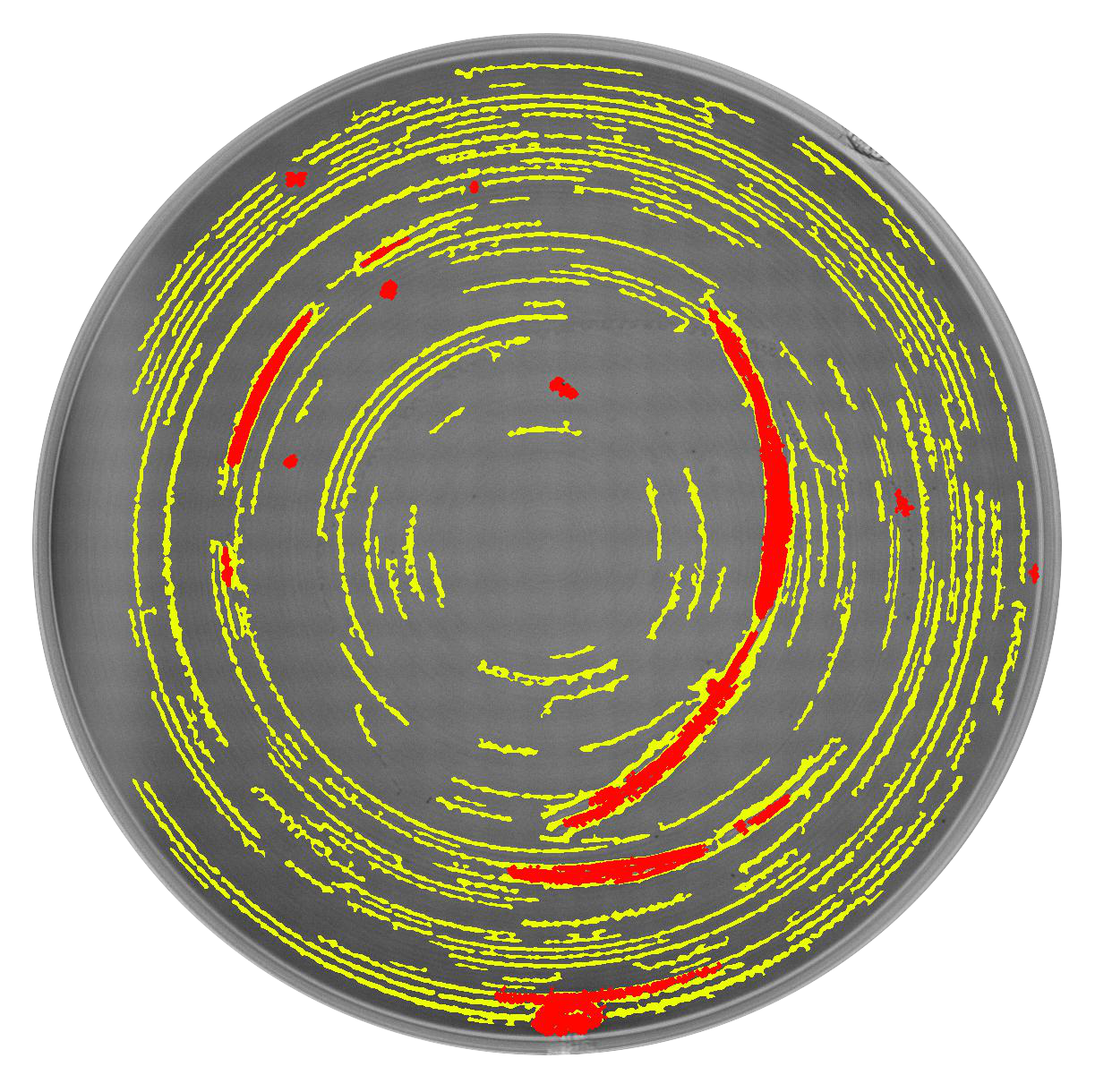
After building a defect library based on QualiLENS® 100 images and providing a short operator training, the test, described above, was repeated. This time, the operator no longer based the assessment on the eyes and binoculars, but on the images output by the QualiLENS® 100.
Outcome
Tests with QualiLENS®100 proved successful, improving consistency from 30% to 70% in repeated measurements by the same operator.
Even with the limited use of the viewer mode, this preliminary stage showcased a dramatic improvement over traditional visual control, leading to more precise and repeatable defect detections.
Our customer decided to implement QualiLENS®100, in viewer mode on their production lines.
The major benefit is a more reliable control process compared to manual inspection, leading to:
- reduced variability and associated costs
- reduced waste and rework
- traceability facilitated by the capacity of the system to store images and report of every inspected lens.
It acts as a bridge to reach the next level of cosmetic inspection with the fully automated defect detection.
“Your technology rocks”
Senior manufacturing engineer
Leading manufacturer of specialty contact lenses