Industry:
Control of reflective surfaces
Reflective surfaces: QualiSENSOR® 100 and 200
On specular surfaces such as automotive body parts, silicon wafesr or sapphire watch crystals, the QualiSENSOR® is best placed to highlight, detect and assess surface defects and features.
The QualiSENSOR® reflection system used for reflection is available in two versions: 100 and 200.
QualiSENSOR® 100 | |
![]() |
|
Measurement range | Up to 170 x 150 mm |
Lateral resolution/ Accuracy / Smallest detectable surface variation |
70 μm < 5 μm < 5μm |
Dimensions (L x W x H) | 500 x 500 x 200 mm |
Weight | Approx. 10 kg |
Power supply | 230/110 V - 16 A |
QualiSENSOR® 200 | |
![]() |
|
Measurement range | Up to 800 x 500 mm |
Lateral resolution/ Accuracy / Smallest detectable surface variation |
70 μm (CdM 170 x 150 mm) 200 μm (CdM 800 x 500 mm < 5 μm < 5μm |
Dimensions (L x W x H) | 1500 x 1300 x 700 mm |
Weight | Approx. 60 kg |
Power supply | 230/110 V - 16 A |
Each user may have different applications and therefore different needs, so we also design customised systems.
Features:
01 Surface characterization
Our full-field measurement system is capable of evaluating minute surface deviations (compared to a perfect surface). The high resolution of our sensors combined with our signal processing technologies allow us to be sensitive to micrometric variations (see below), even on large surfaces.
QualiSENSOR® is suitable for a wide range of industrial applications, such as:
Painting and surface treatments
One of the typical applications is the qualification of the orange peel phenomenon.
The latter is characterised among other things by a specific wavelength as shown below.
Plastic & composite materials
Our systems are used to characterise materials: sink marks, weld lines, surface homogeneity, fibre distribution, etc.
Example of class A surface classification:
The classification of two class A surfaces (300 x 300 mm plate test) at the R&D stage is done in a matter of seconds using the waviness measurement on the QualiSENSOR® 200.
We worked with composite manufacturers et define the quality criteria by correlating the V-Optics waviness index with the customer’s visual perception.
Paper, cardboard and packaging, see Clairefontaine et V-Optics Succès Story
Our solutions allow the inspection and qualification of this type of material.
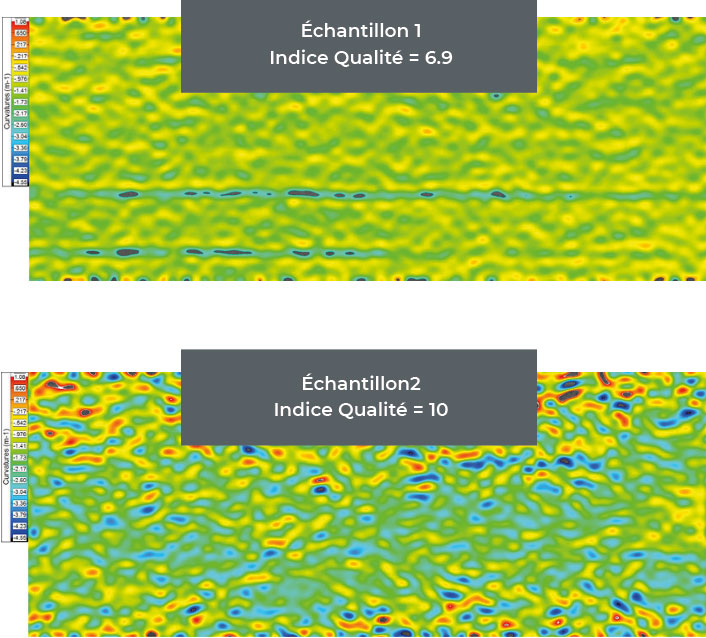
Although paper is not a reflective material, we have installed a QualiSENSOR® 100 at one of our customers’ sites in order to adjust the production tool quickly and optimally.
Here, the QualiSENSOR® 100 tells us that the sample is compliant, because the quality index is less than 7.7 which is the acceptability threshold defined by the customer.
02 Detection of surface defects
The QualiSENSOR® can detect any defect that alters the surface, whether this involves a deviation in shape or a difference in brightness, or reflectivity.

On the image of the left, the polishing defect before painting which is very difficult to see with the naked eye.
On the image on the right, the QualiSENSOR® highlights the frosted area and enables specific automatic detection.
A plastic injection moulding manufacturer wanted to automate its production line inspection using the QualiSENSOR® 200 to scan parts coming off of the press.
The example below shows a class A part rejected by the QualiSENSOR®, following the detection of a scratch too large to be acceptable.
03 Flatness measurement
The QualiSENSOR® is also capable of measuring the flatness of reflective surfaces (mirror, glass, metal, ceramic, etc.).
The example below illustrates the flatness measurement of a silicon wafer 100mm in diameter, in just a few seconds with nanometric precision.
Here are some examples of possible applications:
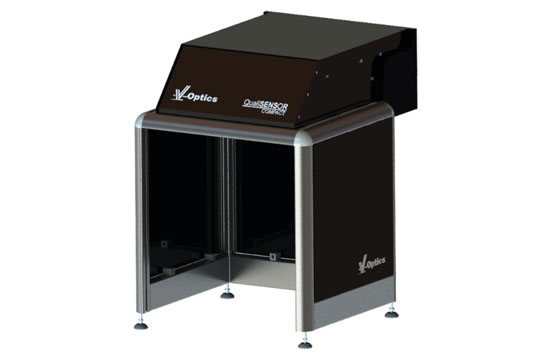
Use of the QualiSENSOR® 100 in off-line and in the laboratory with support to be placed on a table.
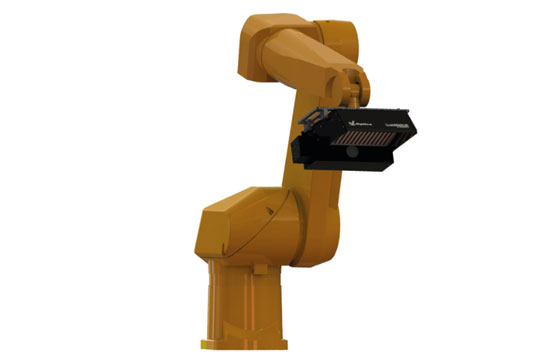
Use of the QualiSENSOR® 100 in production line on static gantry or robotic arm.
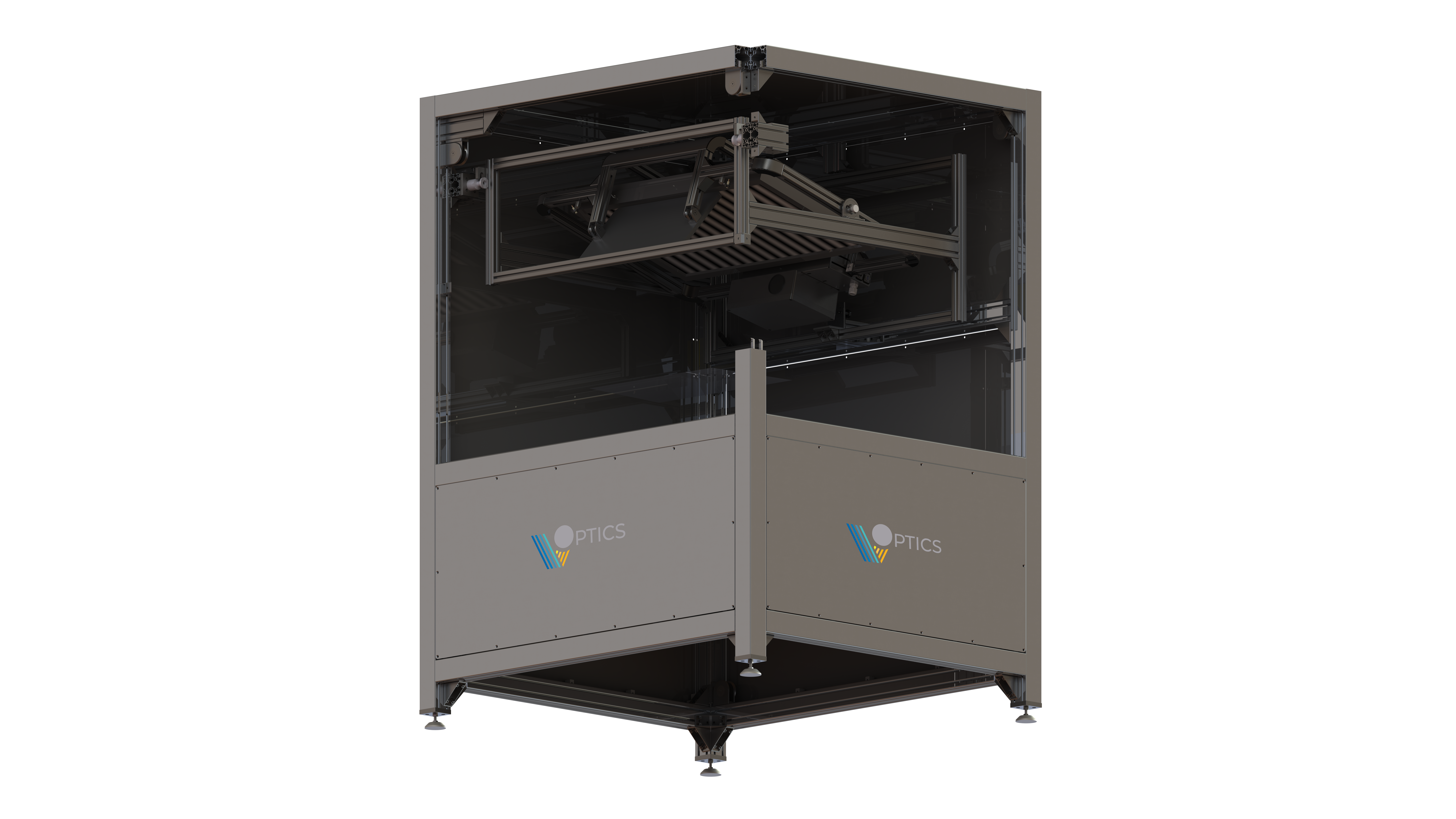
Use of the QualiSENSOR® 200 in off-line and in laboratory, in cabin.
Option on the QualiSENSOR® 200 in the cabin: grazing light function for scanning matt surfaces.
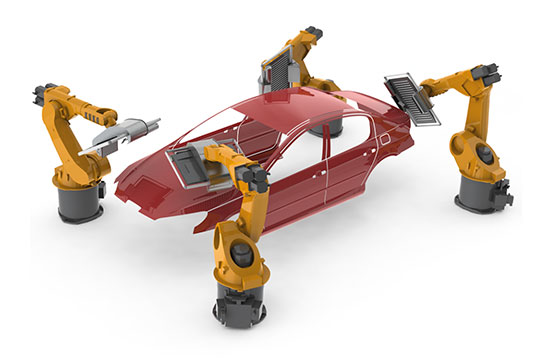
Use of the QualiSENSOR® 200 in production line on static gantry or robotic arm.